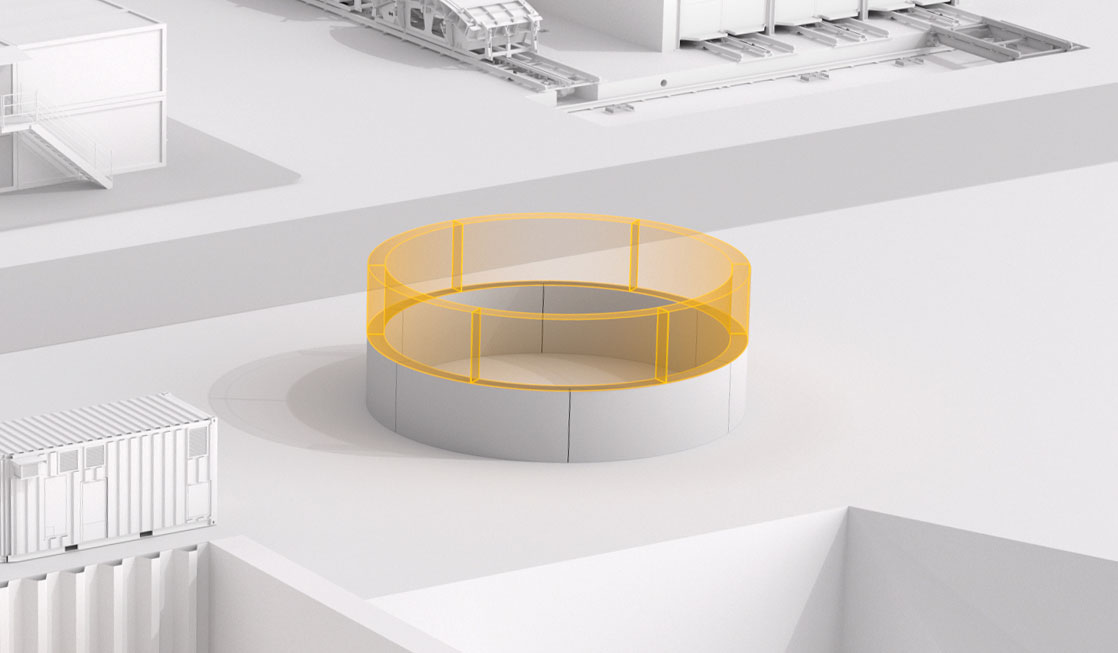
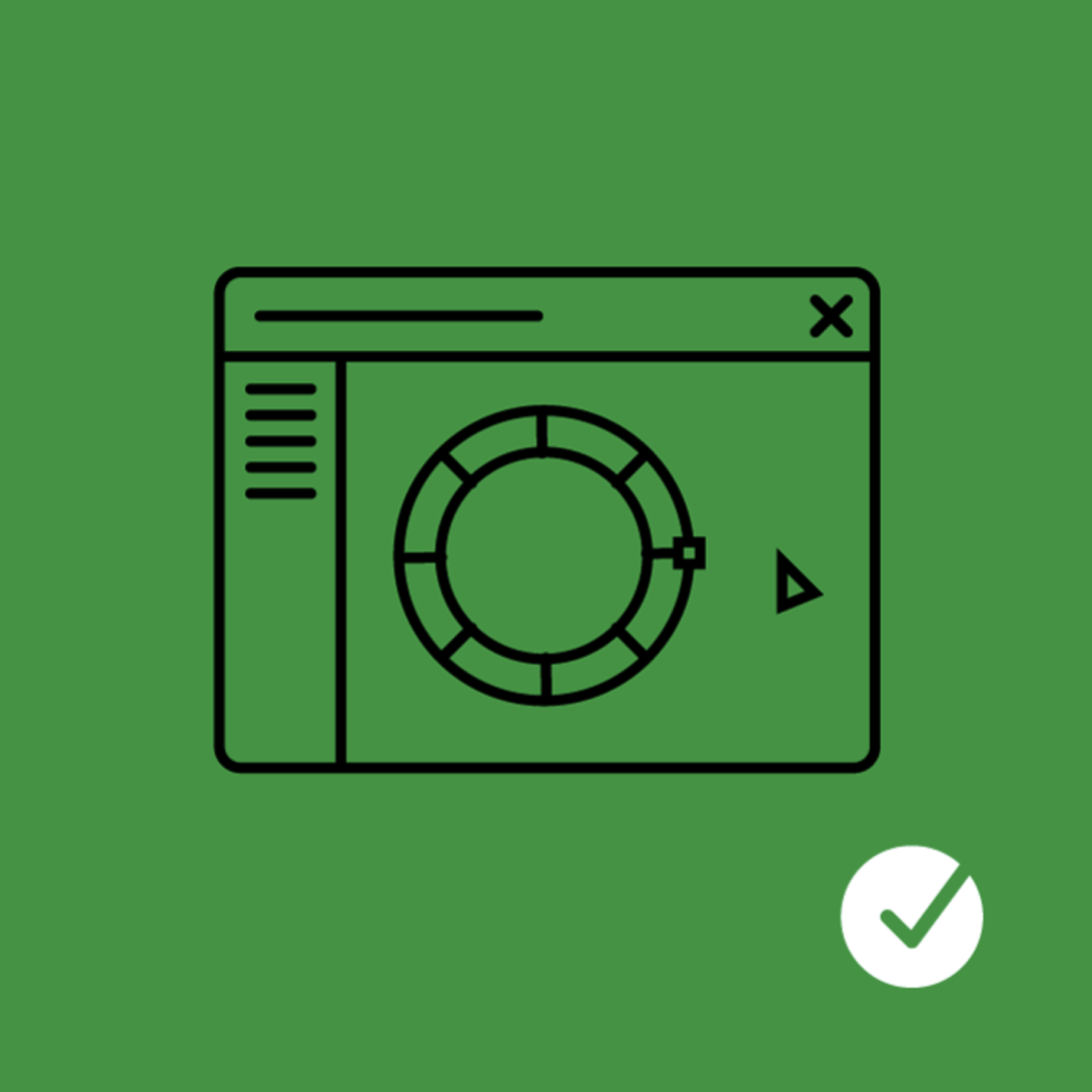
Virtual Ring Building
Virtual Ring Building is a digital process that replaces the physical assembly of master and test ring constructions.
Reason why
The purpose of Virtual Ring Building is to provide a faster, more flexible and safer procedure to prove that the master ring complies with tolerance requirements.
Read more
As proof of compliance with the specified tolerances of the segment rings, building owners or contractors usually require a certain number of test rings to be manufactured before production begins. Traditionally, such test rings are physically built by the site personnel using equipment such as a crane, scaffolding, tension belts etc. With this method, the production of two test rings takes approx. 4-5 days. Facing time, costs and above all the dangerous situations for the personnel, a virtual solution with the same result brings enormous advantages.
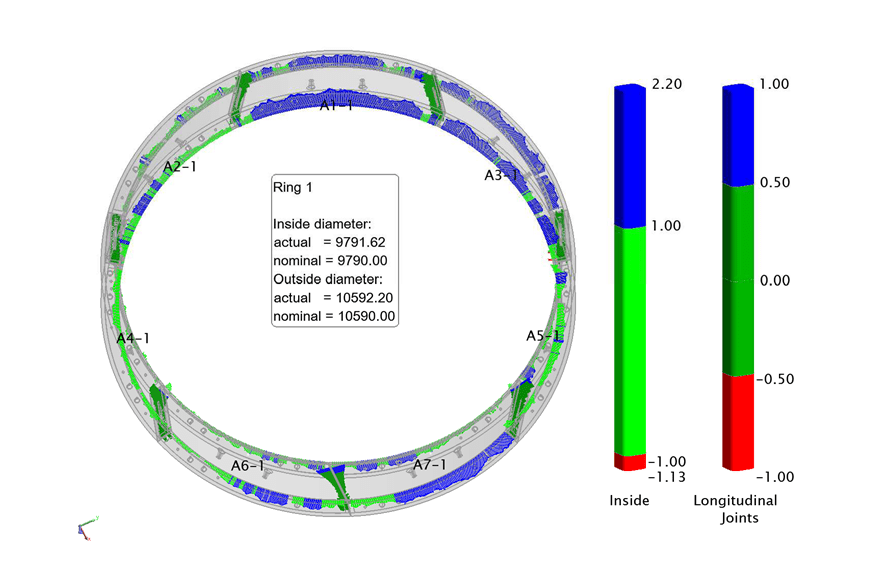
VMT’s Virtual Ring Building procedure bases on a best-fit approach, considering the 3D coordinates from laser tracker measurements of segments or segment moulds. The collected measurement data is output in a report and is available for further calculations and analyses. On the basis of this data, the segments are assembled into a digital ring using 3D software (“ring fitting”) and integrated into a reporting system.
Benefits
- Increased safety
Avoidance of accident risks for the personnel on the construction site. - Time and cost savings
Flexible and fast virtual ring construction on the computer regardless of the location. - Higher accuracy
More accurate measurement as it is unaffected by atypical physical difficulties and limitations of horizontal ring construction.
Customer experience
Project: Northolt Tunnels West HS2
“VMT’s 3D Virtual Ring Build technology was probably chosen for its advanced 3D modelling, accuracy, integration capabilities, and strong support infrastructure. These factors contribute to more efficient and accurate tunnel ring assembly, which is critical for the success of tunnelling projects.”
Loubna Samih
Quality Engineer at Pacadar UK Ltd
Read more
PACADAR U.K. LIMITED was contracted by Skanska Costain STRABAG Joint Venture (SCS) to produce 60,000 segments, each weighing 7 tonnes, to line the 8 km western section of the Northolt Tunnel (S2 WEST) in London. VMT Product Manager Jonatan Rodríguez Marcos spoke to Pacadar UK Quality Engineer Loubna SAMIH about their experience with VMT’s solution for a virtual ring building based on 3D coordinates from laser tracker measurements of segments or segment moulds.
Why did you choose the VMT’s Virtual Ring Build solution based on the LIS 3D geometry check for moulds and segments?
“VMT’s Virtual Ring Build technology was probably chosen for its advanced 3D modelling, accuracy, integration capabilities, and strong support infrastructure. These factors contribute to more efficient and accurate tunnel ring assembly, which is critical for the success of tunnelling projects.”
What were the main arguments that convinced you to rely on VMT’s Virtual Ring Build solution?
“The main arguments of VMT’s 3D virtual ring technology that convinced my team are that it provides detailed guidance and visualisation of the ring assembly process, which leads to faster assembly, reducing project timescales and associated labour costs.”
In general, has the VMT solution met your expectations? Did it perform as expected?
“Yes, the VMT solution generally met our expectations. The system has performed reliably under various conditions and works aligned with what was promised and required.”
What were the main benefits that the Virtual Ring Build delivered, and do you have any ‘hard data’ to demonstrate the benefits, e.g. cost reduction, reduction in manpower/time etc.?
“The Virtual Ring Build provides several benefits, mainly the precision of the segments, efficiency of production, and cost reduction by having the segments right first time which increase precision and reduced rework. Virtual Ring Building reduces the need for manual measurements and adjustments. For the NTW S2 WEST project, Virtual Ring Build has enabled saving of 10% in overall project cost, largely due to the efficiency and precision gains.”
How would you rate your collaboration with VMT?
- in the negotiation/consulting phase
- during implementation
- support during the project
“The negotiation and consultancy phase was smooth as this is the third project we are working with VMT in the UK. During the implementation, the VMT team were very supportive, providing a qualified engineer on site during the commissioning and training.
The VMT 3D virtual ring team are supporting the project, providing several training sessions on the use of the Faro, the software, the measurement of the mould and the segments. They also do TeamViewer sometimes when we have a problem with the 3D laptop.”
Have there been any workflow or synergy benefits from using multiple VMT products on the project – in terms of functionality, support, etc?
“The benefits of using multiple VMT products on the project allow for easier monitoring, management and reporting of our production as expected and required by the client.”
Do you have any suggestions for improving our technologies?
“We have encountered situations where the machine and the reflector lose connection, and the measurement is obstructed. Apart from the annual calibration check, it would be better to have a check every 6 months for the project with daily measurements.”
Would you choose our product solution and VMT as partner again?
“Yes, we would. VMT’s product solutions align with our future goals in terms of performance and reliability, support and service, and product evolution, which is a good reason to continue the partnership.”
Downloads
Our customer experiences provide valuable insights into working with the system.
- Customer experience
Project: Northolt Tunnels West HS2 – PDF
- Product info
PDF-Document
Contact
For more information or project inquiries do not hesitate to contact our expert.
-
Team Leader IMS Service
Dieter Loh