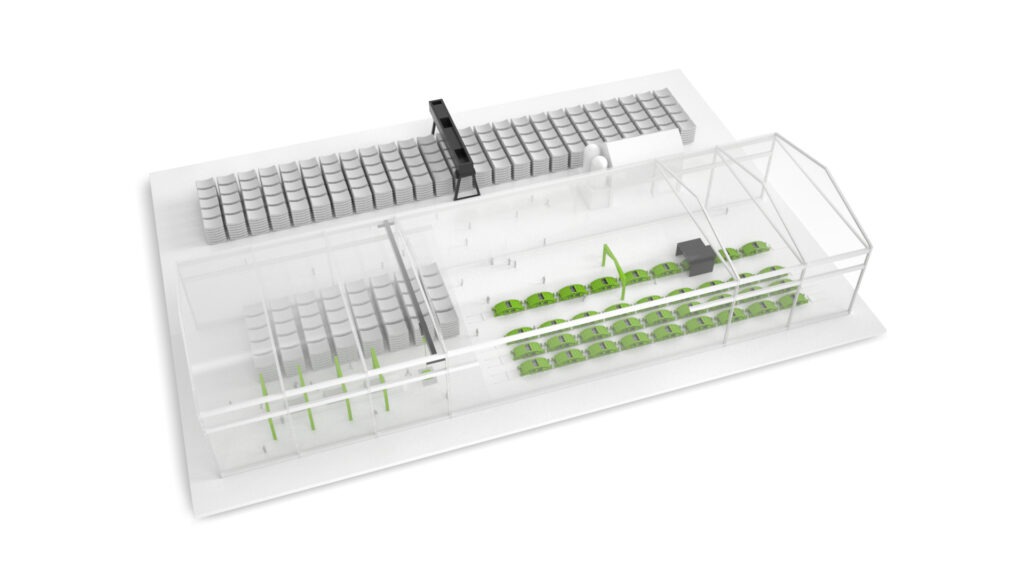
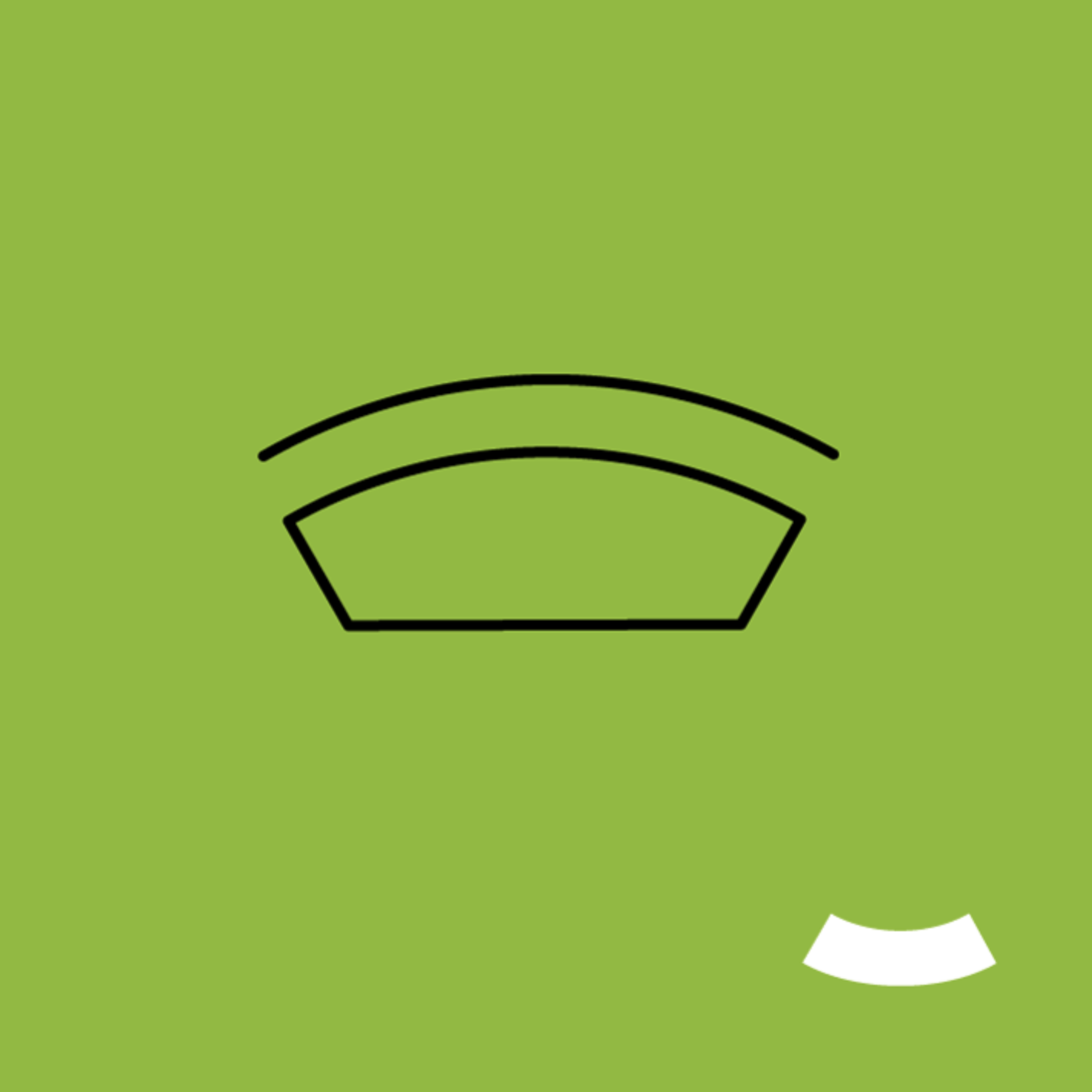
SDS.Stationary
SDS.Stationary is the SDS module that supports planning and documentation for stationary segment production.
Reason why
Read more
With the rising significance of BIM in construction, there’s a growing need for data-driven documentation and management systems in segment production. The primary goal is to identify and counteract errors or weaknesses in the production process. A system is essential that captures and evaluates as much data as possible in connection with the process of segment production.
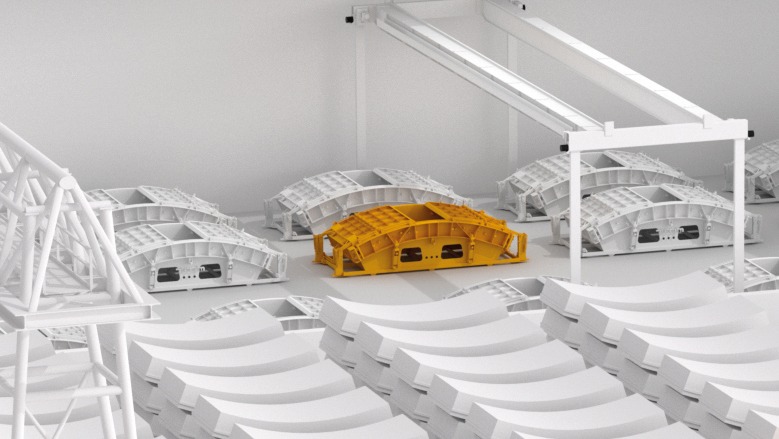
SDS.Stationary assigns a unique barcode label/RFID tag to each produced segment, containing vital data like reinforcement, tools, concrete composition, and segment geometry. Scanners and interfaces record this information. The system not only documents but also specifies and monitors every stage and component of the process.
With a simple button press, the software can generate various evaluations and reports. These serve as crucial discussion and decision-making tools for those in charge.
Benefits
- Reduction in repair, reject and removal costs
Through monitoring and direct feedback, SDS can prevent errors before they happen. - Easier and faster training of new employees
SDS sets out defined stages on the hand-held scanner and takes users through all work stages. - Saving time for documentation
The system creates absolute transparency about the state of the production process at all times. - Fact-based reporting to the client
Thanks to evaluations in seconds and complete, seamless site documentation.
Customer experience
Project: DB Bangalore Metro
“The main benefit of SDS we see is the significant reduction in man-hours compared to a pen and paper/Excel spreadsheet solution. Especially the shift engineers and plant managers workload has dropped down drastically.”
Mohammed Niyas
Larsen & Toubro
Read more
Construction company Larsen & Toubro was contracted to work on the tunnelling of the Bangalore Metro. Following the successful commissioning of the project, VMT spoke to L&T employee Mohammed Niyas to find out his views on VMT’s segment documentation system.
Why did you choose the VMT SDS product when there are alternatives / competitive solutions?
“L&T is in the midst of a digital transformation and is actively looking for arenas to digitise which in turn enhances overall efficiency. Coming to Bangalore Metro, the management, understanding the difficulties of process management with hardcopy / excel data, decided to look for solutions that would digitise the process management of tunnel segment production, storage, dispatch and erection so as to improve quality control and productivity. This search led to VMT’s SDS system and the features provided by it ideally matched our requirements.”
What were the main arguments that convinced you to go with the VMT product?
“SDS offered the full traceability from rebar cage assembly right through to the final installation in the tunnel with special emphasis on production and quality management.”
Did the VMT solution generally fulfil your expectations? Did it perform as expected?
“Once the second phase of installation is completed we fully expect the system to provide a fool proof solution that completely fulfils our expectations. People onsite as well as management are happy to use it. However, on the road to designing the system, we needed to modify it due to additional owner requirements and the complexity of the system solution that was not clear from the very beginning of our investigations. If SDS had a shorter lead time, the configuration could be done closer to the project start which would reduce the need of additional modifications.”
What were the main benefits that the systems delivered and do you have any ‘hard data’ that highlights the benefits, for example cost reductions, reduction in staff/time etc.?
“The main benefit we see is the significant reduction in man-hours compared to a pen and paper/Excel spreadsheet solution. The quality records are collected by the scanners during production and daily reports are generated automatically. We like this, especially as the shift engineers and plant managers workload has dropped down drastically. Moreover, again once the second phase has been completed, we see the SDS system providing a digital back-up of segment production, dispatch and erection data.”
How do you rate your collaboration with VMT?
“Overall the collaboration with VMT was wonderful. The reaction times from the VMT team was very quick, their engineers are patient and have good technical expertise. Writing a specification document up-front to define the system design was very useful to understanding SDS process. To date, whenever needed, we have received quick responses to system outages or when clarification of the process was needed etc. However, the cost of the system exceeded our budget but has proved its worth in the end.”
Do you have any proposals for improvement of our technologies?
“Working with the system, we have noted a number of improvements that might be helpful on future projects. First of all, the implementation of the concrete cubes’ test results (before demoulding, to reach of 24 MPa, after 7 days and after 28 days) and a link to the demoulding time would be a good feature. Also, the management of and an inventory of ‘build-in’ parts such as grout sockets would be useful to control stocks and avoid shortages. In short, a planning module (Inventory, production planning etc.) would make SDS more of a total supply chain management platform we believe.”
Would you opt for a VMT product solution again and work with VMT as a partner?
“Yes, L&T is thinking of using the VMT SDS system for all future segment precast yard operations.”
Video
Downloads
Our product info gives an overview of the features and benefits of SDS. Moreover, our customer experiences provide valuable insights into working with the system.
Customer experience
- Mohammed Niyas
Project: Bangalore Metro – PDF
Product info
- SDS
PDF-Document
Contact
For more information or project inquiries do not hesitate to contact our expert.
-
Head of Project Management
Nadine Fenrich