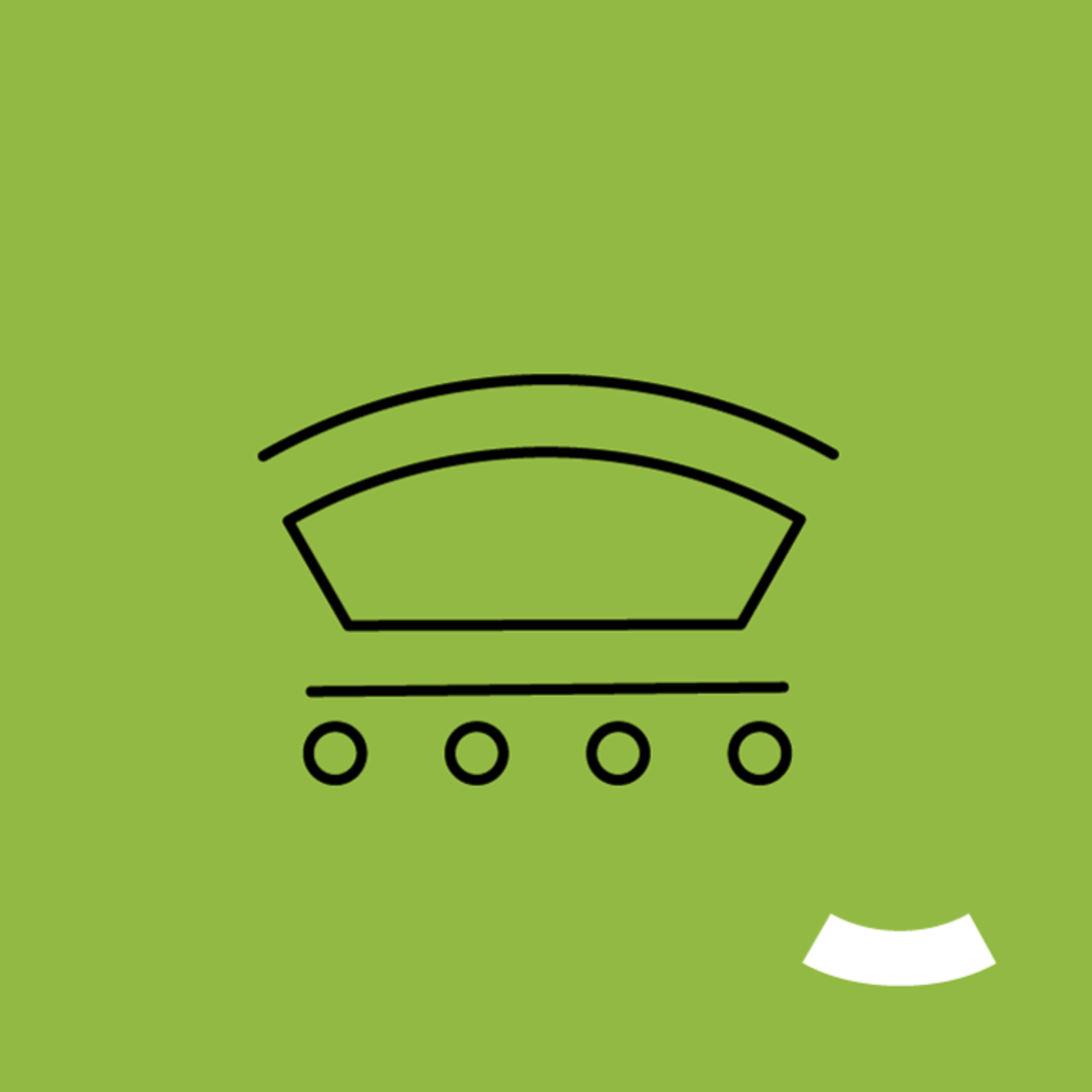
SDS.Carousel
SDS.Carousel is the SDS module that supports planning and documentation for carousel segment production.
Reason why
Read more
With the rising significance of BIM in construction, there’s a growing need for data-driven documentation and management systems in segment production. The primary goal is to identify and counteract errors or weaknesses in the production process. A system is essential that captures and evaluates as much data as possible in connection with the process of segment production.
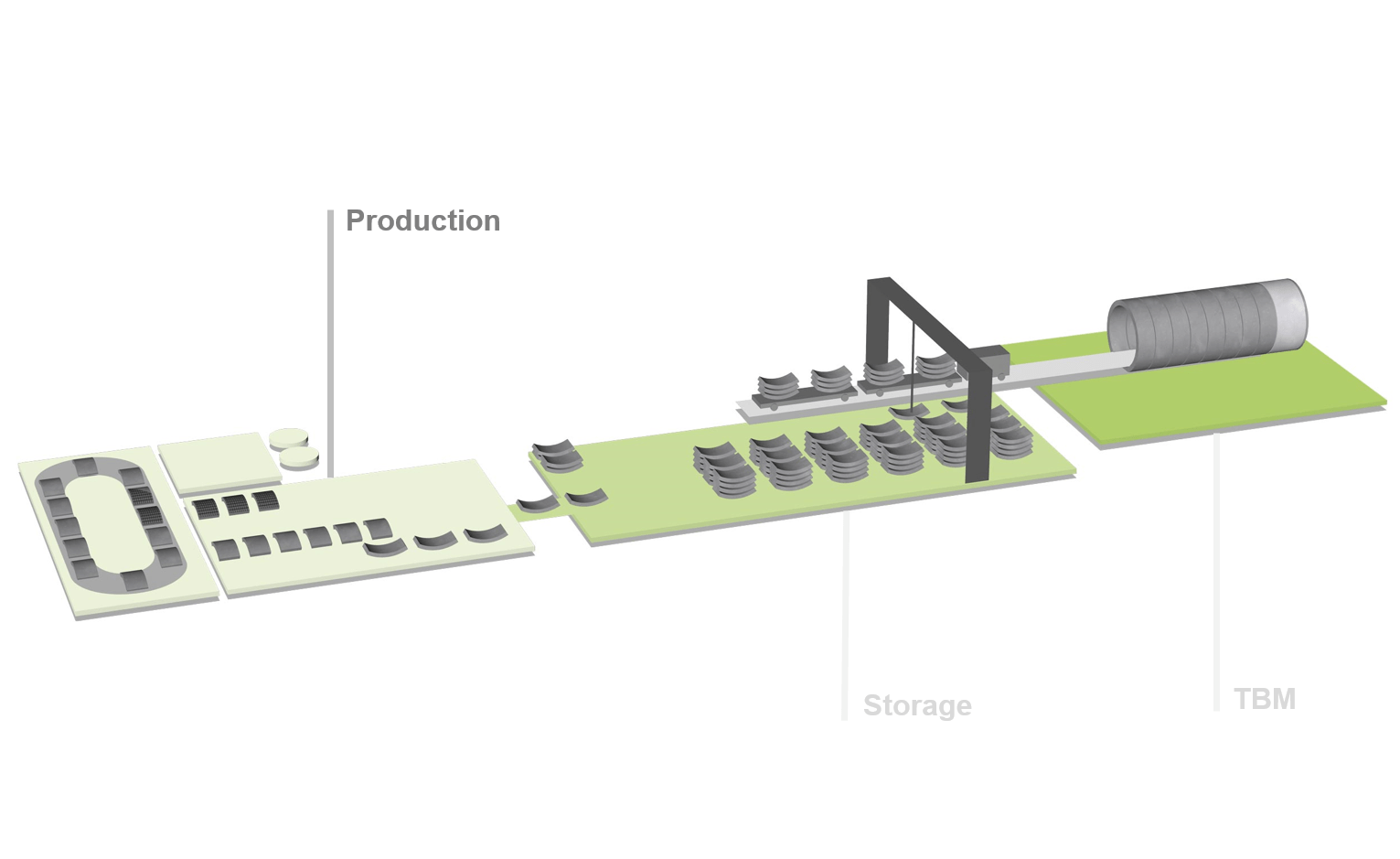
SDS.Carousel assigns a unique barcode label/RFID tag to each produced segment, containing vital data like reinforcement, tools, concrete composition, and segment geometry. Scanners and interfaces record this information. The system not only documents but also specifies and monitors every stage and component of the process.
With a simple button press, the software can generate various evaluations and reports. These serve as crucial discussion and decision-making tools for those in charge.
Benefits
- Reduction in repair, reject and removal costs
Through monitoring and direct feedback, SDS can prevent errors before they happen. - Easier and faster training of new employees
SDS sets out defined stages on the hand-held scanner and takes users through all work stages. - Saving time for documentation
The system creates absolute transparency about the state of the production process at all times. - Fact-based reporting to the client
Thanks to evaluations in seconds and complete, seamless site documentation.
Customer experience
Project: Northolt Tunnels West HS2
“The main benefits have been a significant reduction in project completion time due to the accurate traceability system, which has minimised errors and rework. As everything is implemented in the system, it helps to reduce labour costs by 10%. And certainly, that the SDS has helped us to avoid delays by having everything recorded and tracked.”
Loubna Samih
Quality Engineer at Pacadar UK Ltd
Read more
PACADAR U.K. LIMITED was contracted by Skanska Costain STRABAG Joint Venture (SCS) to produce 60,000 segments, each weighing 7 tonnes, to line the 8 km western section of the Northolt Tunnel (S2 WEST) in London. VMT Product Manager Jonatan Rodríguez Marcos spoke to Pacadar UK Quality Engineer Loubna SAMIH about their experience with VMT’S SDS – Modular Product and Logistics Management System.
Why did you choose the VMT’S SDS – Modular Product and Logistics Management System? Were there any alternatives or competitive solutions?
“We chose the VMT product solution because it offered a complete, comprehensive package that integrated the production process, deformation monitoring and storage of process data. While we evaluated other solutions, VMT’S ability to provide the global process with a variety of options and parameters made them the clear choice.”
What were the main arguments that convinced you to use VMT’s SDS – Modular Product and Logistics Management System?
“The key factor that convinced us was VMT’s excellent customer support and monitoring to customise solutions to our project needs, which played a major role in the user-friendly application.”
In general, has the VMT solution met your expectations? Did it perform as expected?
“Yes, the VMT solution generally met our expectations. The system has performed reliably under various conditions and works aligned with what was promised and required.”
What were the main benefits that the systems delivered, and do you have any ‘hard data’ to
demonstrate the benefits, e.g. cost reduction, reduction in manpower/time etc.?
“The main benefits have been a significant reduction in project completion time due to the accurate traceability system, which has minimised errors and rework. As everything is implemented in the system, it helps to reduce labour costs by 10%. And certainly, that the SDS has helped us to avoid delays by having everything recorded and tracked.”
How would you rate your collaboration with VMT?
- In the negotiation/consulting phase
- during implementation
- support during the project
“The negotiation and consultancy phase was smooth as this is the third project we are working with VMT in the UK. During the implementation, the VMT team were very supportive, providing a qualified engineer on site during the commissioning and training.”
Have there been any workflow or synergy benefits from using multiple VMT products on the project – in terms of functionality, support, etc?
“The benefits of using multiple VMT products on the project allow for easier monitoring, management and reporting of our production as expected and required by the client.”
Do you have any suggestions for improving our technologies?
“I have two suggestions for improving the VMT SDS, one is to implement the final quality status of the product and the second is to provide a solution for the reinforcement if it was reserved during the moulding process.”
Would you choose our product solution and VMT as partner again?
“Yes, we would. VMT’s product solutions align with our future goals in terms of performance and reliability, support and service, and product evolution, which is a good reason to continue the partnership.”
Video
Downloads
Our product info gives an overview of the features and benefits of SDS. Moreover, our customer experiences provide valuable insights into working with the system.
Customer experience
- Loubna Samih
Project: Northolt Tunnels West HS2 – PDF
Product info
- SDS
PDF-Document
Contact
For more information or project inquiries do not hesitate to contact our expert.
-
Head of Project Management
Nadine Fenrich