SDS – at the cutting edge of AI
Concrete segments for large-diameter tunnels must meet stringent quality standards. Due to their size, it is inevitable that defects or damages might occur during production or transportation. Consequently, they undergo multiple checks from the start of production until final installation in the tunnel. However, carrying out an inspection within a TBM is not only challenging because of confined space, but is also labour intensive. Can AI therefore offer a solution?
From mould to tunnel
Transporting multi-tonne concrete segments from the factory to the TBM presents a number of logistical hurdles. Delivered from the storage yard to the TBM using multi-service vehicles or rolling stock, they are temporarily stored in the TBM upon arrival, acting as a buffer until the next delivery. A portal crane retrieves the segments in the correct order from the buffer storage and places them on the segment feeder. The feeder then transports them for the final few meters to the erector. Despite the utmost care, it’s impossible to completely avoid the chance of damage given the challenging working conditions. To streamline subsequent repairs, the segments undergo a critical final quality check before installation, which requires an innovative solution given the space and lighting issues in the tunnel.
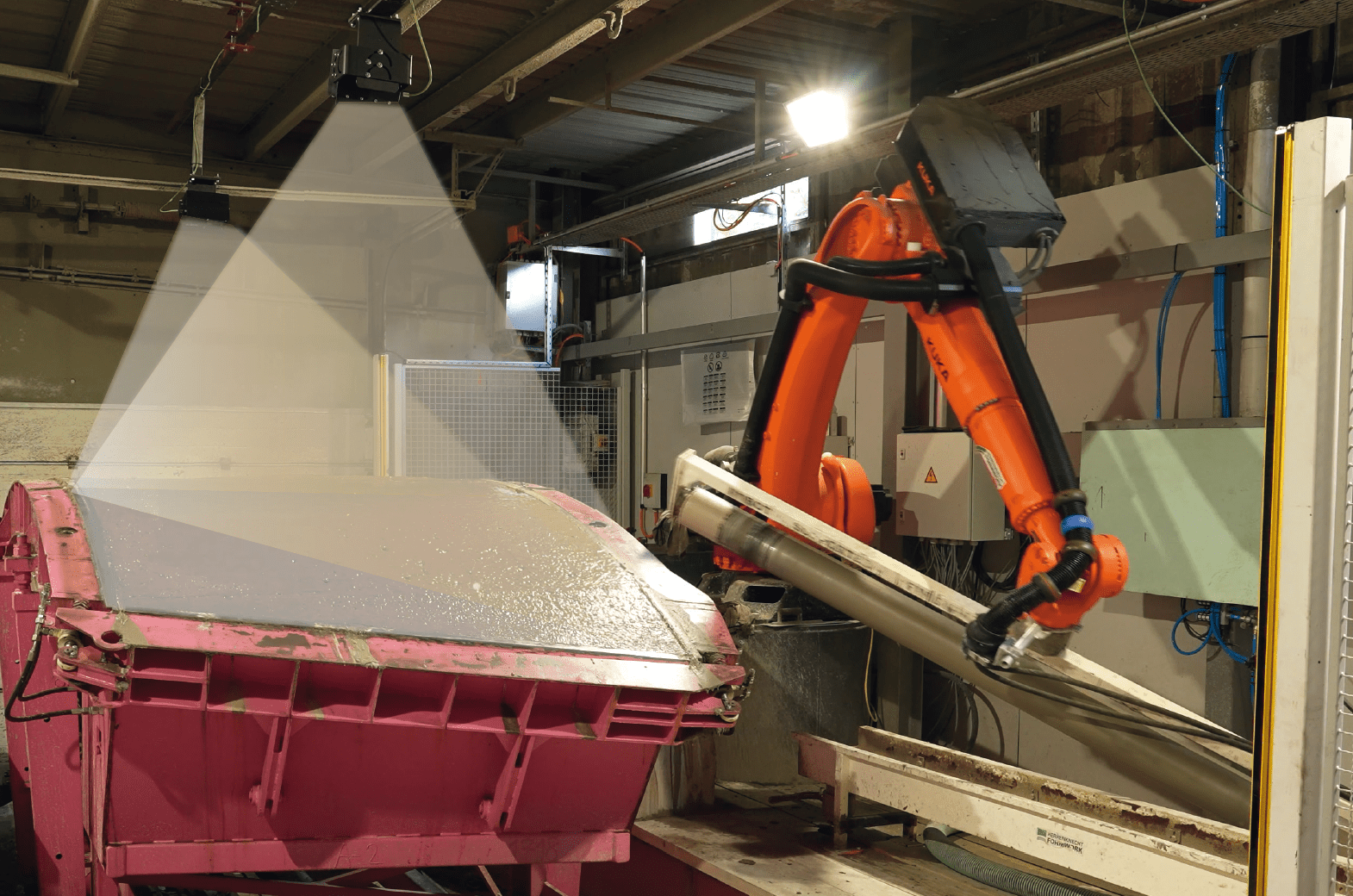
Forward-thinking segment inspection
With a long-term strategic goal of a fully automated excavation process, VMT, in cooperation with an ambitious start-up company, has developed AI-based computer vision software to inspect images of the segments collected by four cameras inside the TBM. The Segment.Check system can accurately detect missing dowels, misplaced seals, cracks and spallings.
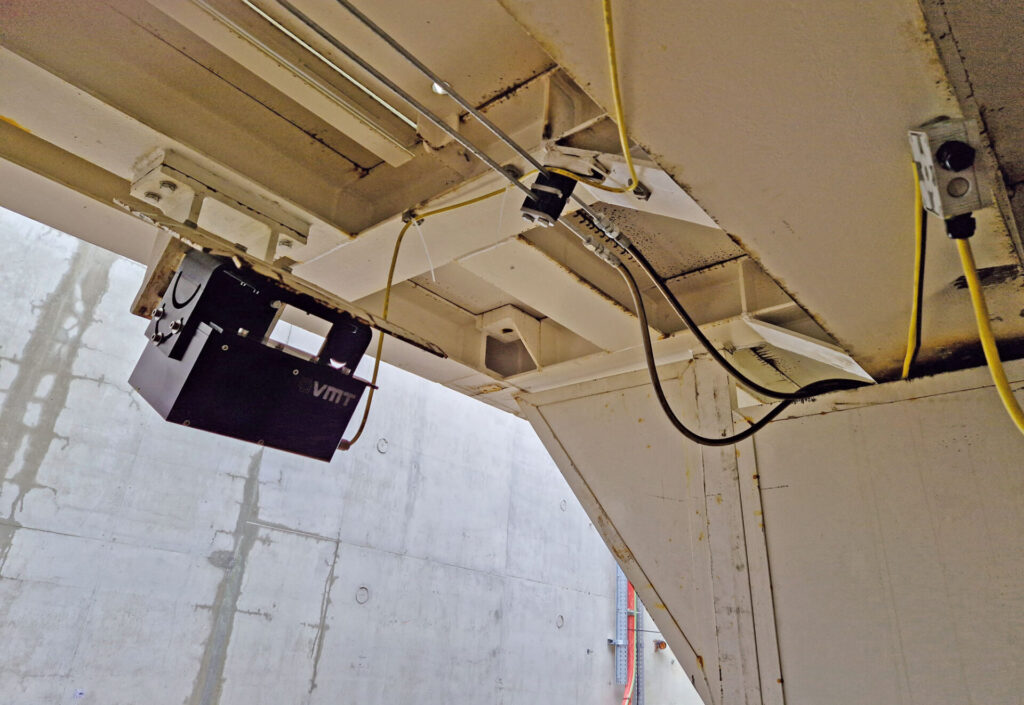
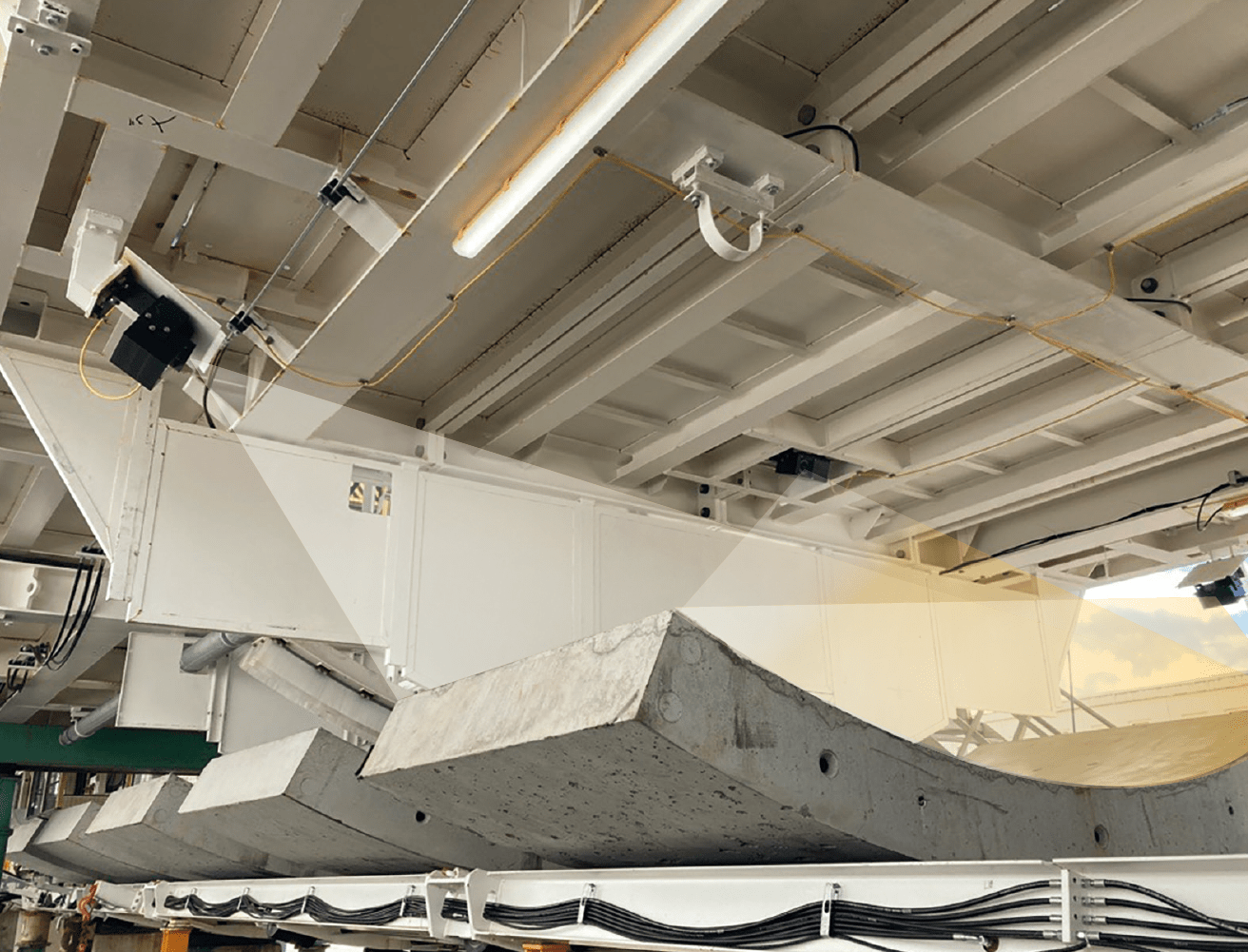
Segment.Check is positioned at the segment feeder, just before the erector, for maximum visibility over the segments. This ensures effective detection of any transport damage even despite dirt, vibrations, high temperatures, humidity and poor lighting in the tunnel. Given the conditions each camera has a custom-made case for the ultimate protection.
The system detects defects and objects, the presence of dowels and the position of seals through neural networks and classification algorithms, which enables defects to be accurately analysed and flagged. The system has already been successfully deployed on two TBMs that are constructing tunnels in London, UK for the HS2 project being constructed by the JV Contractor Costain Skanska Strabag.
Successful human-machine collaboration
A user-friendly dashboard facilitates interaction between humans and machines, providing comprehensive control over the system for TBM drivers and the quality department This dashboard provides easy access to all inspection and operational data, empowering operators to optimize production potential. The Segment.Check data enriches the existing SDS dataset for each segment, providing deeper insights into defect causes and overall quality. It is also compatible with Building Information Modelling (BIM).
Continuous improvement efforts aim to expand the system to include inspecting the side facing towards the tunnel wall and incorporating additional sensors such as 3D cameras or lidar technology.
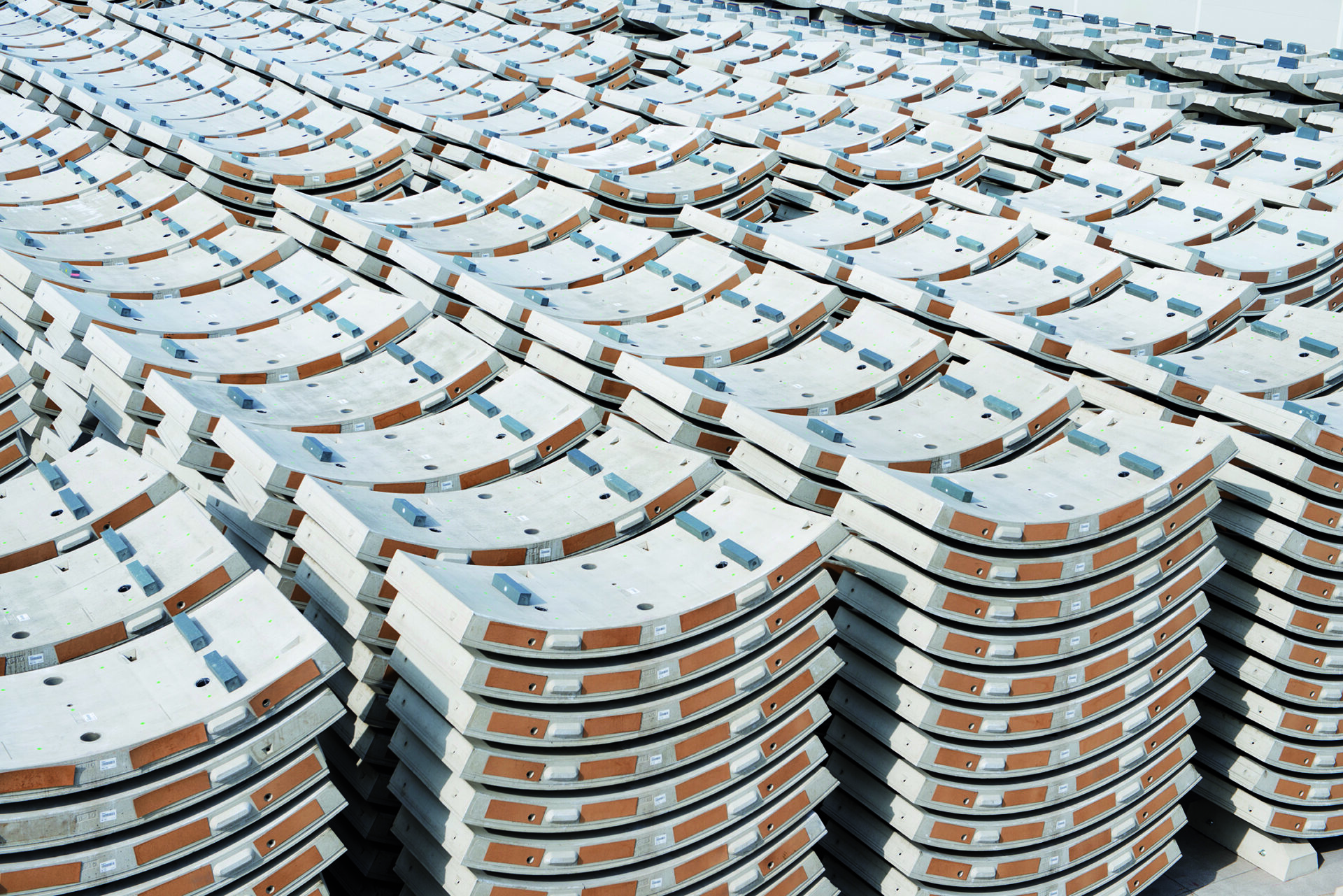