From physical to virtual: Tunnel lining master and test rings
Virtual Ring Building offers a faster and more flexible method for verifying that master and test rings meet tolerance requirements. But, is it possible to completely replace the physical construction of test rings? Yes, it is and there are also compelling advantages.
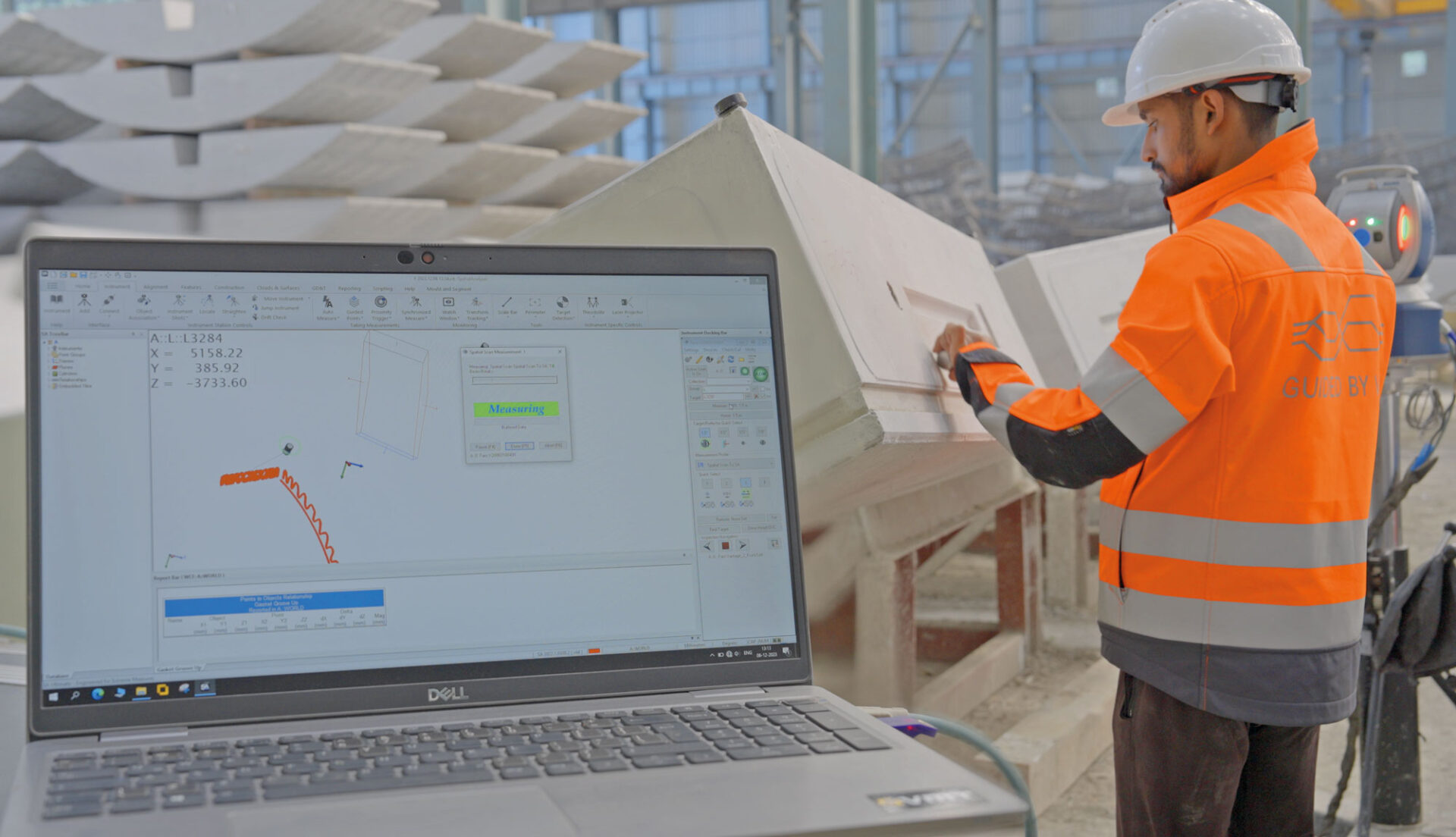
Virtual Ring Building
For decades, tunnel projects with segmental lining have involved casting segments and erecting master rings horizontally on a flat surface to ensure compliance with dimensional tolerances. Requirements for master and test rings vary by project, sometimes necessitating additional concrete rings as trial rings. Master and test ring construction is challenging and risky, especially for large-diameter tunnels and often requires a truck-mounted crane and takes up to a week. Different tolerances, including manufacturing and spatial tolerances, impact the final geometric result. To improve casting quality, a tool focusing solely on dimensional tolerance is needed and this can be achieved through virtual rings.
Replacing a tradition
Virtual master rings can switch the traditional horizontal assembly of segments from physical to digital. Using 3D coordinates from laser tracker measurements, virtual segments can be rapidly ‘assembled’ into rings, ensuring sub-millimetre accuracy and checking bolt-hole alignment. This digital approach focuses on casting quality and avoids the risks and inaccuracies of physical assembly, such as the non-simulation of tunnel conditions. VMT has used the technology in 20 projects to date, including London’s Thames Tideway and Switzerland’s Gotthard Road tunnel, which both use virtual rings to various extents and demonstrate its reliability and effectiveness.
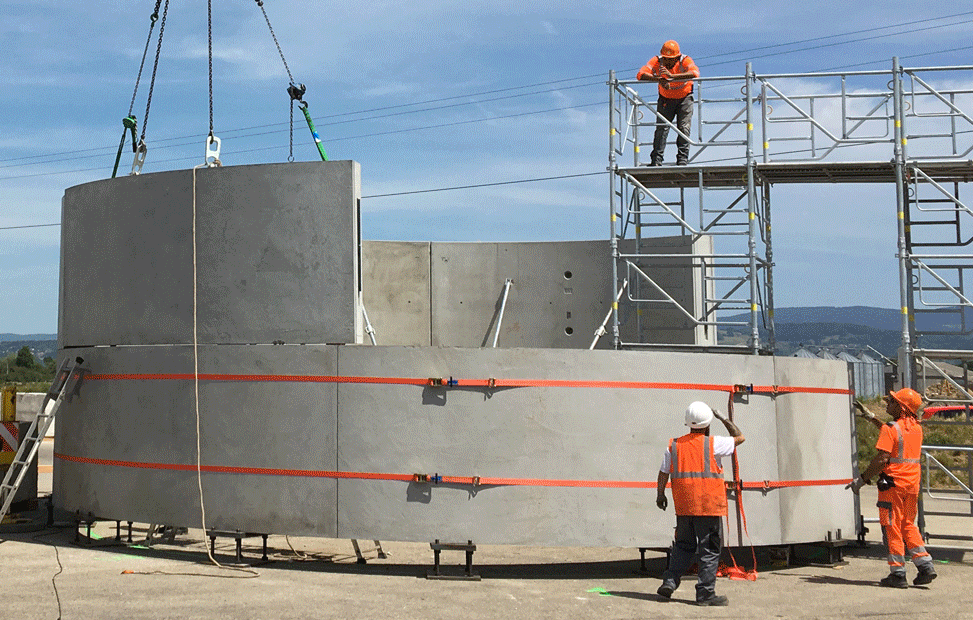
A virtual mathematical process
The 3D measurement scan data of each mould or cast concrete segment is combined mathematically to assemble the bored tunnel lining ring, known as a Virtual Ring Build. This is achieved through mathematical relationships, enabling dynamic inspection, alignment, virtual fit-up, real-time assembly and optimisation. These relationships calculate and recalculate the distance between entities when moved, efficiently linking multiple points and objects. For a virtual ring, calculations include fitting measured points to nominal dimensions and ensuring no overlaps at joints. The results, showing deviations and gaps, are presented graphically, highlighting variations from theoretical measurements.
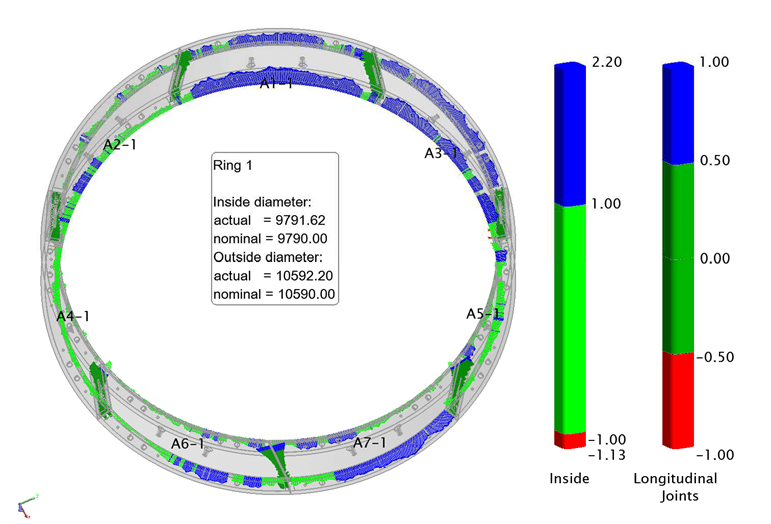
What may sound highly theoretical actually offers practical advantages, such as improved quality control, elimination of construction inaccuracies and proactive problem-solving. It demonstrates the compatibility of segments from various mould sets, reduces rejection rates, saves time and costs, and eradicates health and safety risks for onsite personnel.
Learn more about Virtual Ring Building