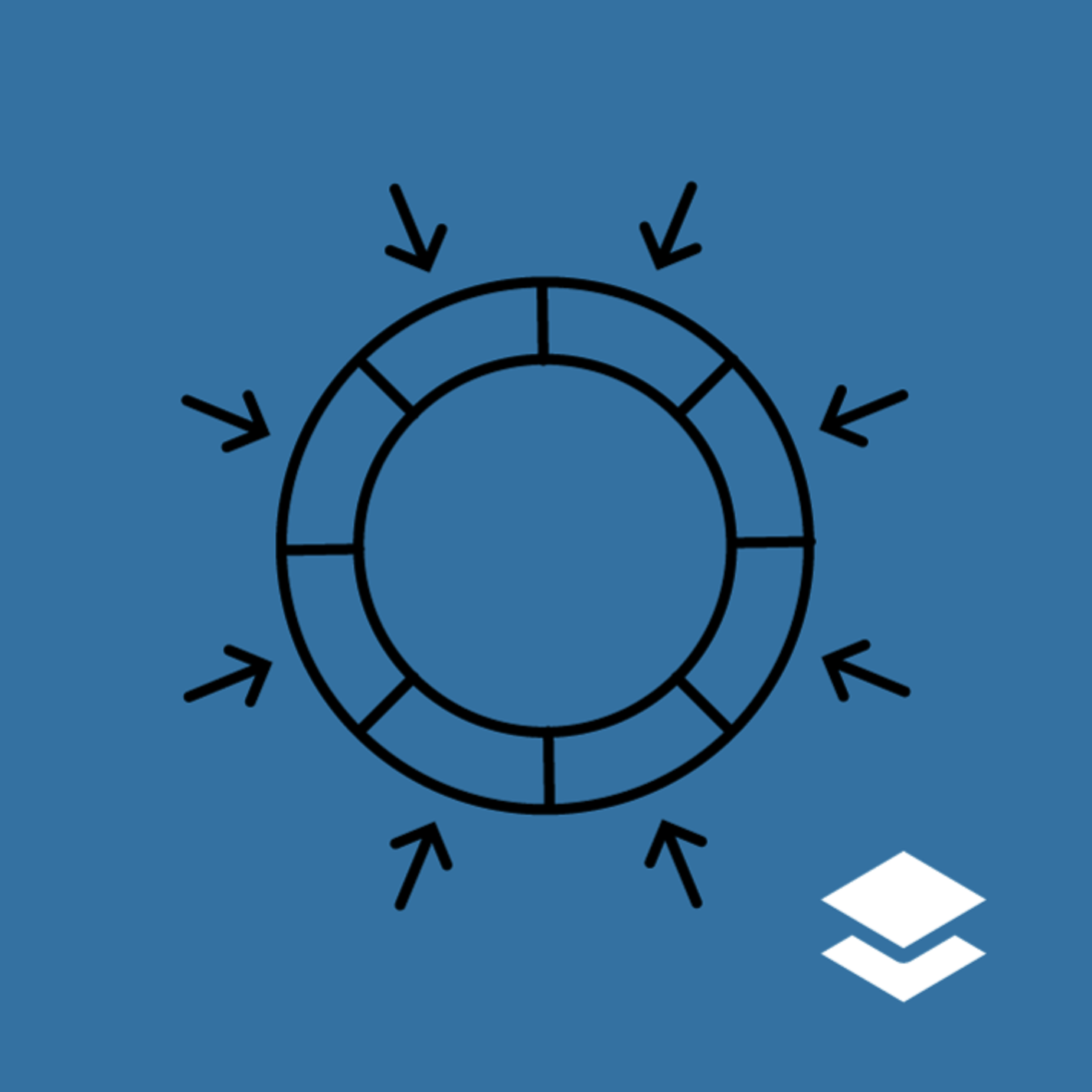
Ring Convergence Measurement System RCMS
RCMS is an automatic ring convergence measurement system optimised for tunnelling projects with segmental lining.
Reason why
The purpose of RCMS is to automatically measure ring convergences in segmental lining tunnelling projects that might occur due to vergences, i.e. deformations resulting from environmental pressures (rock pressure, annular gap injection) after installation of a ring.
Read more
Manual measurements are often constrained due to ring building or obstruction by the gantry. If injection occurs solely behind the machine, manual recording of ring deformation becomes impossible. In such cases, automated measurements emerge as the sole effective solution.
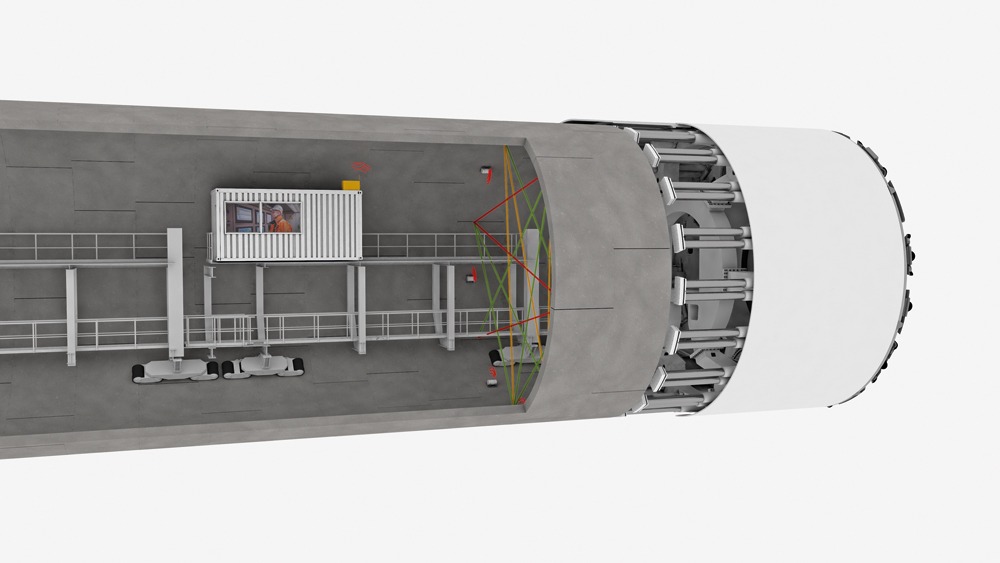
Conclusions about occurred deformations of the ring can be drawn from a possible change in inclination of the observed segments. Therefore, a small inclination sensor (inclinometer), is mounted on all segments of the rings to be monitored. The sensors transmit their data by radio to a central data logger, who then relays it to the logging computer where the data is evaluated and archived.
In addition, the data can easily be transferred to further systems, such as TUnIS Navigation Office.
Benefits
- Quality always in view
Deformation of already built rings are detected early to support the quality of the tunnel structure. - Reduced personnel expenses, complete overview
Automatic data acquisition and the simplification of monitoring, logging and archiving act to streamline processes and increase transparency. - Quick installation and deinstallation
Wireless communication of the system components, battery operation and gluing of the reusable, non-segment-damaging sensors minimise time expenditure. - Early control
Unlike conventional manual methods, measurement starts immediately after ring completion to detect convergences directly after leaving the tailskin. - Measurements with added value
In contrast to conventional convergence measurements, RCMS records all ring segments in the gantry area. This ensures precise and thorough measurement of the entire ring.
Customer experience
Project: DB Project Stuttgart
“The system has offered us better and more stable functionality as well as hardware savings, as well as having the advantage of having a direct contact person.”
Thomas Unterfeld, Survey Coordinator
Implenia Construction GmbH Tiefbau
Read more
The DB Project Stuttgart in Germany is a rail development connecting Stuttgart and Ulm which includes the restructuring of the Stuttgart node and a new line from Wendlingen to Ulm. As part of this project there are some 63.4 km of cuttings and tunnels, which includes the Albvorlandtunnel Los 2 project which is being constructed by Implenia Construction GmbH Tiefbau and Tunnelbau Deutschland.
As part of the tunnel construction operation the contract called for continual measuring of the tunnel support ring convergence. Dipl.-Ing. Thomas Unterfeld, Measurement Coordinator was in charge of selecting and managing the right measurement system for the project. He chose VMT’s RCMS (Ring Convergence Measurement System). Interviewing Thomas Unterfeld about the project he was asked:
Why did you decide to use RCMS for this project?
“The service description of our contract demands the monitoring by means of a measuring system for the continuous monitoring of ring convergence. As there were no comparable alternatives in terms of similar performance spectrum or promise from other manufacturers and given that we were familiar with the RCMS predecessor from a previous project, we decided to go with RCMS in its new further-developed and optimised version. The main arguments for the VMT RCMS system that convinced us to move forward with this product was our experience of the company’s reliable employees and the availability of full system support when required and the stability of the RCMS. So far the system has fully met our expectations.”
Did RCMS provide additional capabilities over the course of the project?
“By using the two new systems, which we had already used in their test phase and which could still be optimised to our project requirements, we were able to achieve significant improvements in respect of our monitoring process. For example assembly times were shortened substantially and the resources needed were also reduced. Instead of 2 or 3 persons working for 2 hours or more, the assembly requirement was reduced to 2 persons working for a maximum of 15 minutes.”
How would you summarise your experience with RCMS system and VMT?
“The direct selection of the RCMS meant that we were able to facilitate the necessary requirements of our particular system quickly and efficiently with our needs being achieved by VMT under strict time limitations. The installation process was excellent and the ongoing support cannot be faulted. The system has offered us better and more stable functionality as well as hardware savings. There is also the advantage of having a direct contact person. Ultimately we have to date been extremely pleased with the modifications to the basic system provided by VMT to ensure our system fitted our purpose exactly. Would we use RCMS again? Yes, most definitely, particularly as it would partner us again with the VMT team.”
Downloads
Our product info gives an overview of the features and benefits of RCMS. Moreover, our customer experiences provide valuable insights into working with the system.
Customer experience
- Thomas Unterfeld
Project: DB Project Stuttgart – PDF
Product info
- RCMS
PDF-Document
Contact
For more information or project inquiries do not hesitate to contact our expert.
-
Regional Sales Manager
Jonatan Rodriguez Marcos