SDS – auf dem neuesten Stand der Technik mit KI
Betonsegmente für Tunnel mit großen Durchmessern unterliegen strengen Qualitätsanforderungen. Aufgrund ihrer Größe ist es unvermeidlich, dass während der Produktion oder des Transports Fehler oder Beschädigungen auftreten. Deshalb werden sie vom Beginn der Produktion bis zum endgültigen Einbau in den Tunnel mehrfach kontrolliert. Die Inspektion innerhalb der Tunnelbohrmaschine ist jedoch nicht nur aufgrund der beengten Platzverhältnisse schwierig, sondern auch arbeitsintensiv. Kann KI hier eine Lösung bieten?
Von der Schalung in den Tunnel
Der Transport der tonnenschweren Betonsegmente vom Werk zur TBM ist mit einer Reihe logistischer Hürden verbunden. Die Tübbinge werden mit Multiservice- oder Gleisfahrzeugen vom Lagerplatz zur TBM geliefert und dort zwischengelagert, wo sie bis zur nächsten Lieferung als Puffer dienen. Ein Portalkran holt die Tübbinge in der richtigen Reihenfolge aus dem Pufferlager und legt sie auf den Segmentfeeder. Dieser transportiert sie dann die letzten Meter zum Einbauort. Trotz aller Sorgfalt sind Beschädigungen unter den erschwerten Arbeitsbedingungen nicht ganz auszuschließen. Um spätere Reparaturen zu vereinfachen, werden die Tübbinge vor dem Einbau einer letzten kritischen Qualitätskontrolle unterzogen, die angesichts der Platz- und Lichtverhältnisse im Tunnel eine innovative Lösung erfordert.
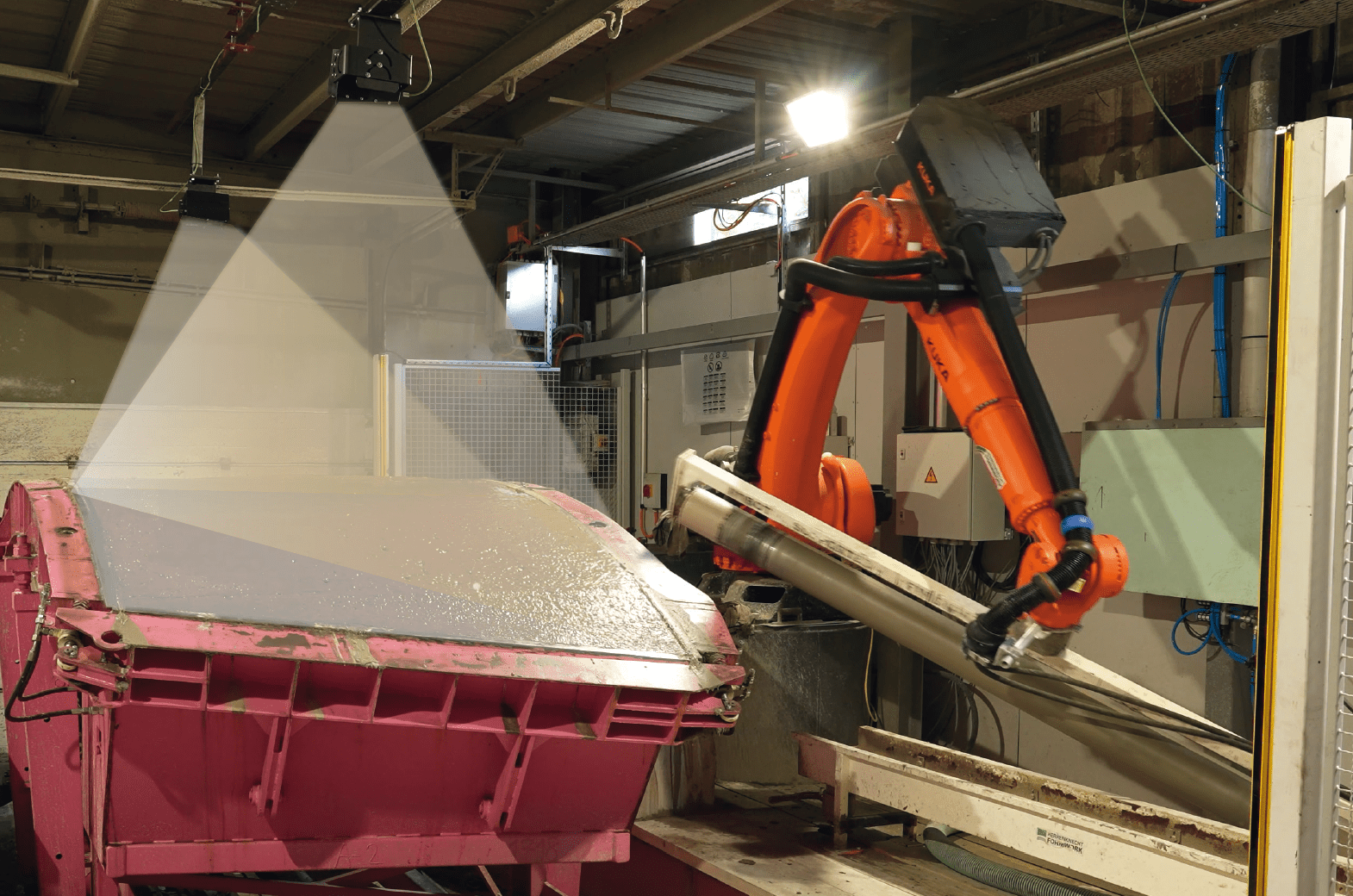
Zukunftsweisende Segmentprüfung
Mit dem langfristigen strategischen Ziel eines vollautomatischen Vortriebsprozesses hat VMT gemeinsam mit einem ambitionierten Start-up-Unternehmen eine KI-basierte Bildverarbeitungssoftware entwickelt, um die von vier Kameras im Inneren der Tunnelbohrmaschine aufgenommenen Bilder der Tübbinge zu überprüfen. Das System Segment.Check ist in der Lage, fehlende Dübel, falsch platzierte Dichtungen, Risse und Abplatzungen präzise zu erkennen.
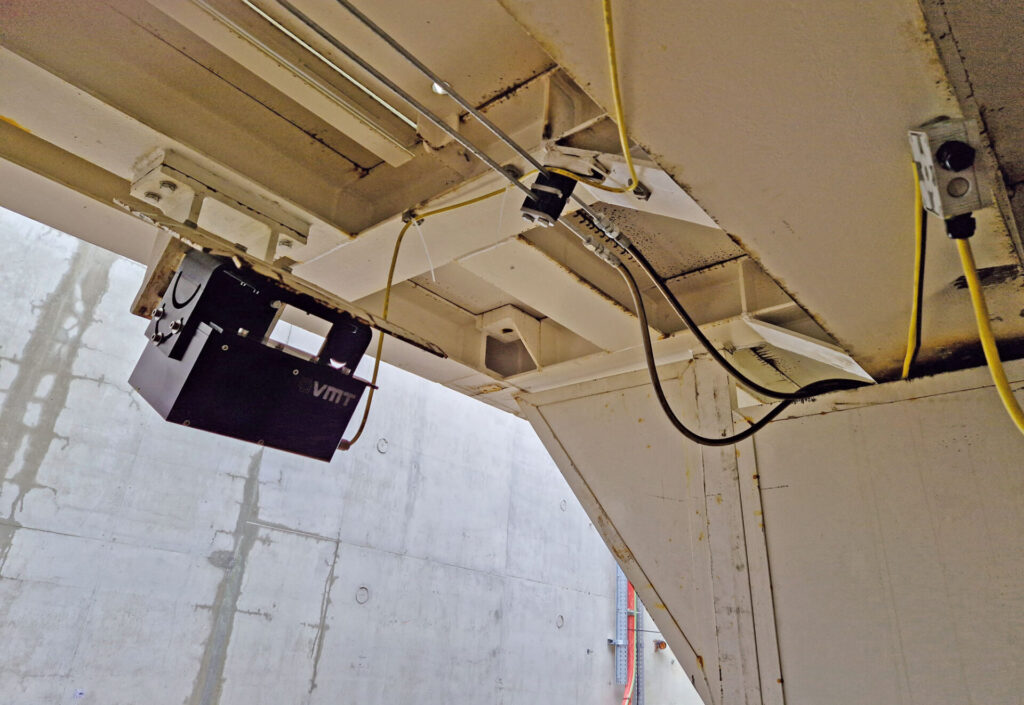
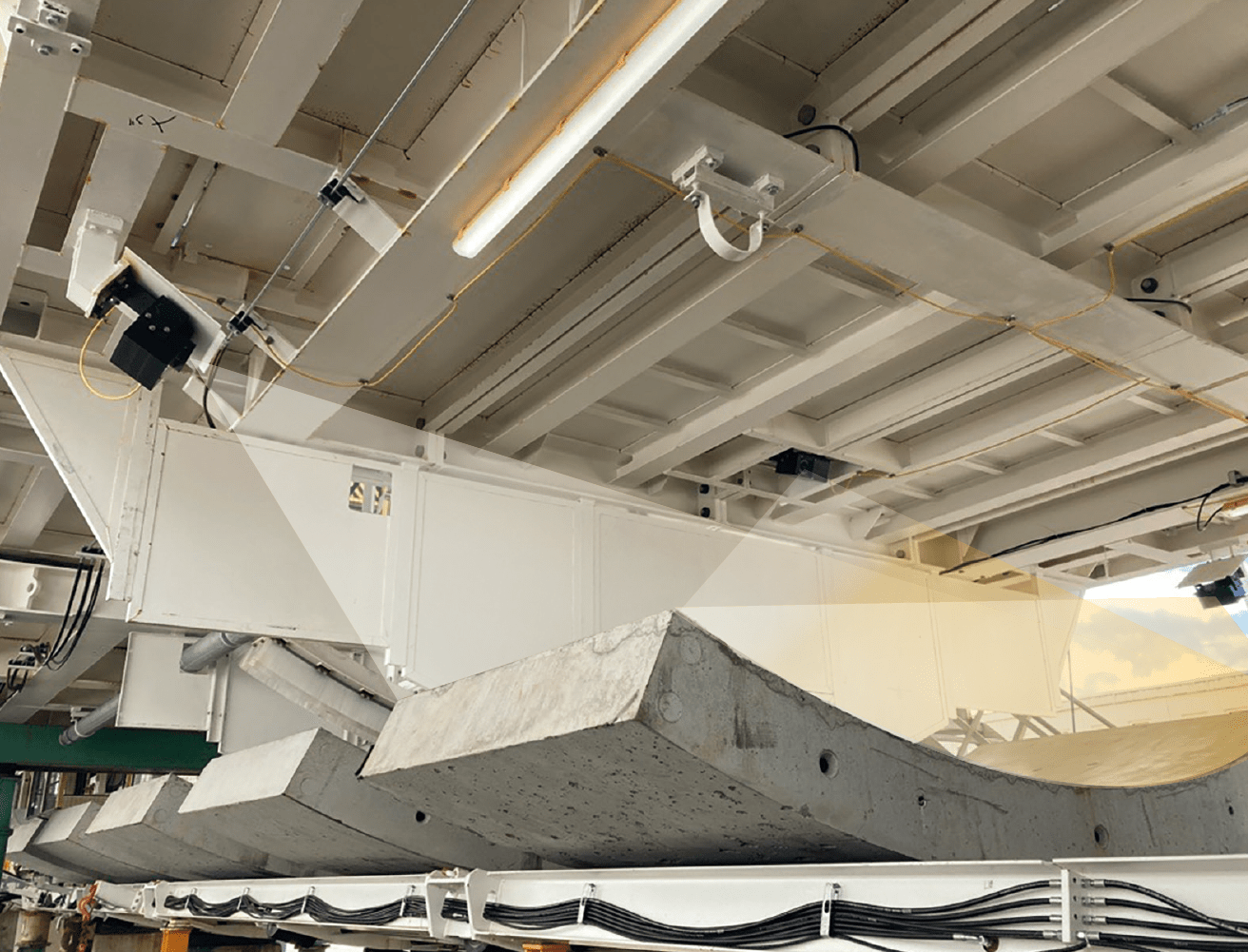
Segment.Check wird am Segmentfeeder kurz vor dem Erektor positioniert, um eine maximale Sicht auf die Tübbinge zu gewährleisten. So können Transportschäden trotz Schmutz, Vibrationen, hohen Temperaturen, Feuchtigkeit und schlechter Beleuchtung im Tunnel erkannt werden. Jede Kamera verfügt über ein speziell angefertigtes Gehäuse, das bestmöglichen Schutz bietet.
Das System erkennt Defekte und Objekte, das Vorhandensein von Dübeln und die Position von Dichtungen mit Hilfe von neuronalen Netzen und Klassifizierungsalgorithmen, wodurch Defekte genau analysiert und identifiziert werden können. Segment.Check wurde bereits erfolgreich auf zwei Tunnelbohrmaschinen für das HS2-Projekt des Baukonsortiums Costain Skanska Strabag in London eingesetzt.
Erfolgreiche Zusammenarbeit von Mensch und Maschine
Ein benutzerfreundliches Dashboard erleichtert die Interaktion zwischen Mensch und Maschine und gibt sowohl den TBM-Fahrern als auch der Qualitätsabteilung die volle Kontrolle über das System. Das Dashboard bietet einen einfachen Zugang zu allen Inspektions- und Betriebsdaten und ermöglicht es den Bedienern, das Produktionspotenzial zu optimieren. Die Segment.Check-Daten ergänzen den bestehenden SDS-Datensatz für jedes Segment und bieten einen tieferen Einblick in die Fehlerursachen und die Gesamtqualität. Sie sind auch mit Building Information Modeling (BIM) kompatibel.
Durch kontinuierliche Verbesserungsmaßnahmen soll das System erweitert werden, um auch die der Tunnelwand zugewandte Seite zu inspizieren und zusätzliche Sensoren wie 3D-Kameras oder Lidar-Technologie zu integrieren.
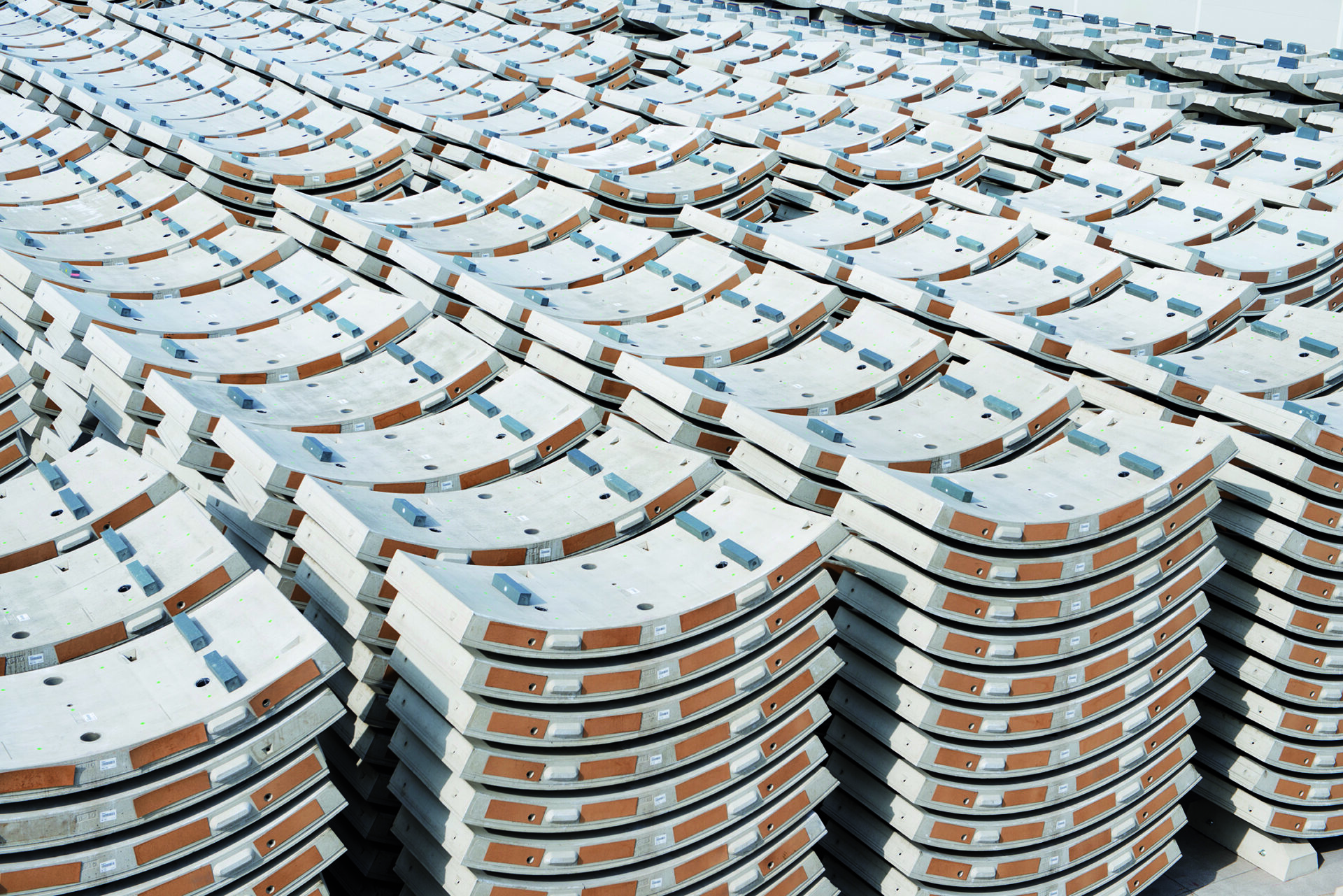